Just recently I decided to build a DIY island to go in my guest house. I really wanted a cedar topped island, but knew that this was not the typical countertop material for an island. But, I decided that I would go ahead with the project and try to demonstrate how to easily throw one of these together using only wood materials that can be found at any big box store. Because this project is so in depth, I have also decided to separate it into two parts. This is part one (the island). I will be placing a link to part two (the table top) at the end of this article.
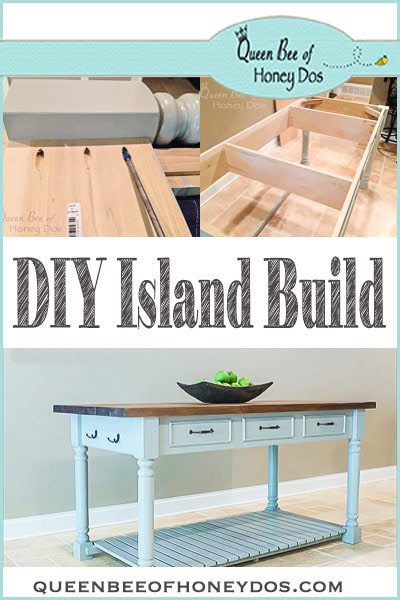
Materials Used for the DIY Island…
- 4 legs cut to 34″ high (I used some old stair posts, but even a simple 4×4 post will work)
- 2 pieces of 1″x7″ cut to 58″ in length (You can just get a 6′ section and leave it, if you prefer)
- 2 pieces of 1″ x 7″ poplar cut to 24″ in length
- 2 pieces of 1″ x 7″ wood cut to size for center support
- 4 corner braces (can be cut from scrap wood or metal braces can be used)
- 2 pieces of 1″x 2″ poplar cut to 61″ (for bottom rails)
- 19 pieces of 1″ x 3″ wood cut to 27″ for bottom slats (I just used scrap whiteboard, but just about any wood will work if you are painting, as long as it is straight and blemish free)
- 2 pieces of 1″ x 3″ wood cut to size (for outer bottom slats – if everything is square these should be right at 24″, but because the post blocks can vary slightly, measure each piece individually)
- 1 piece of 1″ x 3″ wood cut to size (for rails’ support)
- decorative trim (optional)
- pulls and hooks (optional)
- primer and paint (more about this below)
- wood putty
Tools that I Used for the DIY Island…
- miter saw (If you have everything precut at the hardware store you can probably get by with just a manual miter box or even a circular saw
- nail gun (you could also get by with a hammer and finishing nails)
- Kreg Pocket Hole jig
- drill/screw driver
- 3M sanding blocks in medium grit
- 2″ kreg pocket hole screws
- 1 1/4″ kreg pocket hole screws
- square
- paint brushes
- tack cloth
DIY Island Build…
These are my posts and aprons after I had cut everything down to size. As noted above, I used some old stair posts for my legs. I simply removed enough from the longer blocked end to allow my apron to comfortably attach. I then removed the amount needed from the shorter block to get the post down to 34″. (Note – if you are using a post that has a top block portion that is less than 7″, you will need to use a different width for the apron. The apron must be able to fit completely on the flat surface). If you want to get posts that are like mine and can’t find any – try these legs from Osborn’s. The poplar wood that I used came from Lowe’s (Home Depot also carries these). I made sure that each piece was in perfect condition – straight with no bowing or defects. These are in the top choice (furniture) wood section.
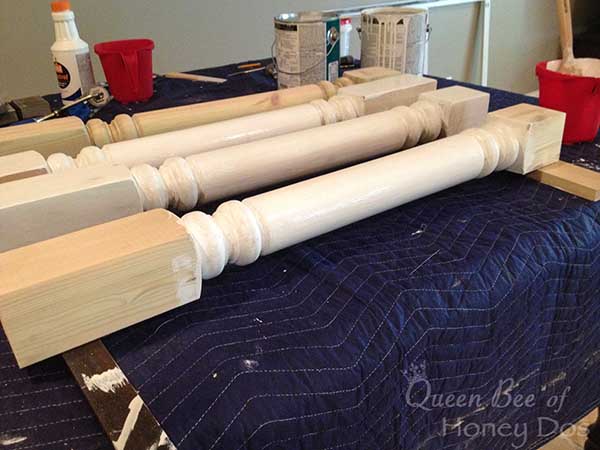
Next I primed and painted the wood. Yes, that’s right. I painted before assembling. To get a good finish on the posts, I set the block ends on scrap wood. This allowed me to rotate the posts as I painted the curved centers.
Here, you can see how I painted around the rounded areas of the post. I did not try to go up and down the length at all. I just rolled the post and kept steady pressure with the brush.
A note on How I Paint…
Moving On…
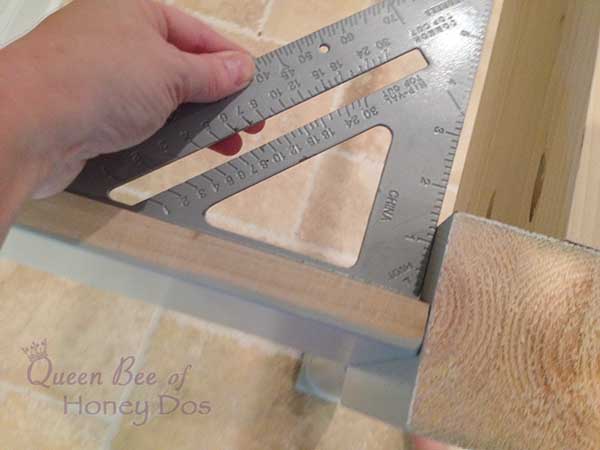
Repeat for each end, and then the front and back apron sections. I used a square to check each section. (It is very important to make sure that the frame is completely square before preceding).
ANyway, Back to the DIY Island…
– PIN IT –
– PIN IT –
Linked up with Remodelaholic
Please keep it clean. Comments that do not follow the Comment's Policy may be removed.